Personal Protective Equipment (PPE) Safety Training
Summary
Personal Protective Equipment (OSHA 29 CFR 1910.132 & 1926 Subpart E): Each employer is required to perform and document a hazard assessment of the workplace to determine if hazards exist that make the use of personal protective equipment (PPE) necessary. If so, appropriate PPE must be selected.
(1) Training is required and includes:
1. When the PPE is necessary,
2. What PPE is required,
3. How to use the PPE,
4. The limitations of PPE, and
5. Proper care and maintenance of the PPE.
(2) Each affected employee shall demonstrate an understanding of the training specified in paragraph (f)(1) of this section and the ability to use PPE properly before being allowed to perform work requiring the use of PPE.
(3) When the employer has reason to believe that any affected employee who has already been trained does not have the understanding and skill required by paragraph (f)(2) of this section, the employer shall retrain each such employee. Circumstances where retraining is required include, but are not limited to, situations where:
1. Changes in the workplace render previous training obsolete, or
2. Changes in the types of PPE to be used render previous training obsolete; or
3. Inadequacies in an affected employee’s knowledge or use of assigned PPE indicate that the employee has not retained the requisite understanding or skill
Hazard Identification and Assessment
One of the “root causes” of workplace injuries, illnesses, and incidents is the failure to identify or recognize hazards that are present, or that could have been anticipated. A critical element of any effective safety and health program is a proactive, ongoing process to identify and assess such hazards.
To identify and assess hazards, employers and workers:
Collect and review information about the hazards present or likely to be present in the workplace.
Conduct initial and periodic workplace inspections of the workplace to identify new or recurring hazards.
Investigate injuries, illnesses, incidents, and close calls/near misses to determine the underlying hazards, their causes, and safety and health program shortcomings.
Group similar incidents and identify trends in injuries, illnesses, and hazards reported.
Consider hazards associated with emergency or nonroutine situations.
Determine the severity and likelihood of incidents that could result for each hazard identified, and use this information to prioritize corrective actions.
Some hazards, such as housekeeping and tripping hazards, can and should be fixed as they are found. Fixing hazards on the spot emphasizes the importance of safety and health and takes advantage of a safety leadership opportunity. To learn more about fixing other hazards identified using the processes described here, see “Hazard Prevention and Control.”
Training Videos
Please view all videos using the "PREVIEW' version first.
If you decide a video is what you are looking for in training a group of your employees, you can then download the high resolution video version. This is important because the WV LTAP is charged per high resolution view of both the “English” and “Spanish” videos.
We are happy to offer these videos at no-cost to the local and state public works and roadway agencies located within West Virginia. Using the "Preview" version when evaluating videos allows us to keep our costs down and allows you to watch the complete video, just at a lower quality. The "Preview" version will still work great on a computer screen and helps us keep costs down and continue this program.
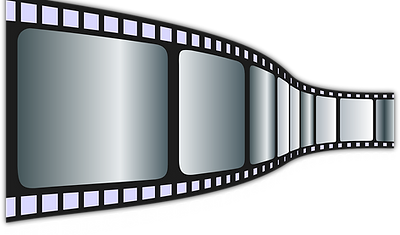